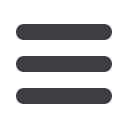
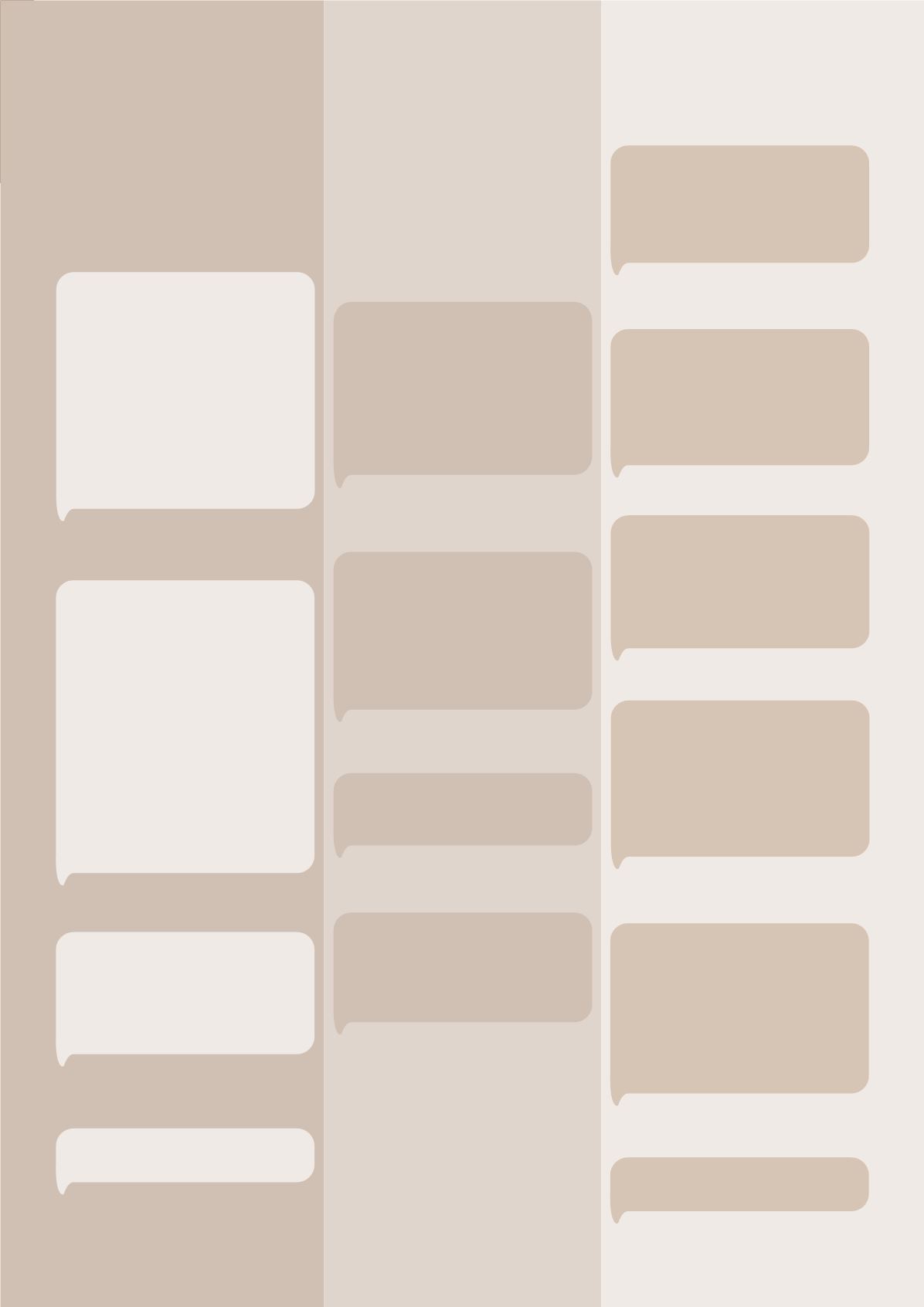
In our case, until now, besides contro-
lling direct costs by their nature, at the
same time and at the project’s internal
level, we monitored actual costs incu-
rred every month based on the project
work units of the project under con-
tract. In this way, we had the necessary
information to control the variations
that could exist in respect of the direct
planned cost and to know at all times
the profit/loss margin on the sale of
the work unit with respect to the cost
incurred.
José Luis del Valle
Project Manager, Arroyo de la
Charca-Grimaldo joint venture
Benito Romero
Project manager/Cataluña Civil Works
Antonio Dámaso
Project Manager,
Setúbal Conservation
Antonio Dámaso
Project Manager,
Setúbal Conservation
José Luis del Valle
Project Manager, Arroyo
de la Charca-Grimaldo joint venture
Juan Ignacio Cuñado Sandoval
Head of the Distribution Networks,
Madrid
José Manuel Torres Corral
Project Manager of Viviendas
Montealiso
Oscar Fernández
Project Manager, San Claudio WWTP.
Benito Romero
Project Manager, Cataluña Civil Works
José Manuel Torres Corral
Project Manager of Viviendas
Montealiso
José Luis del Valle
Project Manager, Arroyo
de la Charca-Grimaldo joint venture
Benito Romero
Project Manager,
Cataluña Civil Works
Juan Ignacio Cuñado Sandoval
Head of the Distribution Networks,
Madrid
José Manuel Torres Corral
Project Manager of Viviendas Montealiso
Until December 2014, costs per unit/
operations was not controlled, at least
officially. Each project team made es-
timates of the most important units
that had to be executed every month
and every four months and the cost
variations per SIE nature, to correct, if
necessary the planned cost in the up-
dating.
As of January 2014, with the collabo-
ration of the Control Unit, we started
to allocate direct costs to each of the
operations defined in the operations
catalogue which basically coincided
with the units in the budget of the
project.
Positive. Even though at the beginning
data to be processed and analysed in-
crease, it will make it possible to make
a rigorous analysis on a monthly basis
and at the conclusion of the contract
of the actual cost per operation. In
addition, it will be possible to obtain
historical data on the unit cost per
operation which will make it easier to
manage current and future contracts
with the client and the subcontractors.
In the medium term, it will ensure that
we have comprehensive knowledge
of the costs per operation and, what’s
most important, in the future this in-
formation will be available not just for
the project, but also for the entire cor-
porate structure.
I think that having a single tool and
that the fact that the criteria for moni-
toring costs is the same for all of the
Company’s projects will help us not
only to be able to control costs on a
monthly basis, but also will enable us
to have a large database that we can
use to plan future projects.
It significantly improves management
since it facilitates the decision-ma-
king process in the short and medium
term for developing the different acti-
vities that we carry out in our projects
on a daily basis and in the future, it will
allow us to know the actual cost of a
series of activities which will enable
us to present more realistic offers to
our clients.
It offers the advantage of being able
to know the price of things within the
system.
In our specific case, since we apply
a system, it provides an extra control
for comparing against our system
even though it will be able to check
every day, on real time, the evolution
of costs, making it possible to know
ahead of time if there is a variation in
a project unit and the measures can
be taken more promptly.
I believe that if it is well managed, it
will be quite useful since it gives you
an idea, immediately of where you
have to take steps as a priority, trying
to optimise costs if possible, and also
lets you know to whom you have to
address any claims.
It will take some time for the change
to be effective but, in a few months,
with proper training, it will be easily
assimilated.
Considering that the procedure is not
unknown to us, the only thing we have
to do is become familiarised with the
functioning of the work tool to be able
to put it into practice.
We believe that it is a question of ha-
ving the entire project team involved,
from the project manager to the ad-
ministrative staff, from the production
managers to, of course, the project
manager, and that we are all able to
have the same name for the same
item which will make allocation easier,
which is the basis for the success of
this system.
Until now, we did not planned the
operations and the cost control was
done according to the nature of the
cost (manpower, sub-contractors, in-
dustrial, etc.) using a software tool
adapted to our needs.
The control was performed outside
the system especially the industrials.
What did you do up to now
to control actual costs
per planned operations?
What is your opinion on
the change of culture
implied by the allocation
of resources to
the operations?
How does this tool impro-
ve project management?
What does it contribute?
On-site interviews